[ad_1]
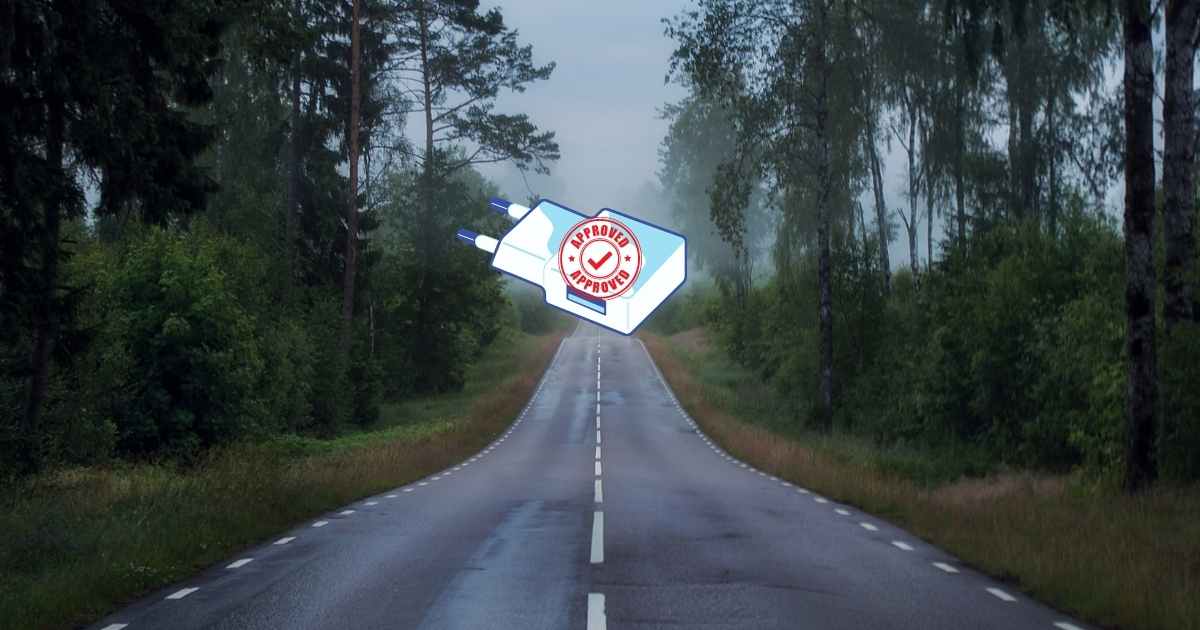
In almost all instances, people who find themselves growing a brand new {hardware} product are likely to overestimate the progress they’ve already achieved, relative to the “end line” (bringing a batch of completed merchandise to market). They typically assume the toughest is to get to a prototype that works like and appears like, the ultimate desired product.
That’s typically flawed, as getting tooling and pre-production pilot runs signed off could take extra effort and time.
Equally, they typically assume they’ll get to that remaining, accredited, prototype quickly. A lot before is reasonable… and even of their greatest curiosity.
Let me clarify.
Easy product vs. new and complicated product
If you’re designing, say, a barely extra elegant design of a salt & pepper set, it might probably nonetheless be a quite simple product. It could not trigger any main challenges in both its design or manufacturing, so long as the supplies are ‘meals protected’.
Now, if you’re designing an digital gadget that can present the optimum mixture of oil & vinegar with a number of modes, and with the power to maintain the liquids at an optimum temperature, attending to a remaining prototype is a unique story. (To make clear: it’s an imaginary product…however who is aware of, it might exist already!?)
There’s complexity in designing the electronics and within the programming. There’s issue in choosing the precise elements/modules. There’s substantial testing to do. The form of the enclosure may need to be re-designed as a way to allow plastic injection molding. And so forth and so forth.
I’m not even mentioning regulated merchandise (e.g. medical gadgets, automotive equipment…) or significantly advanced merchandise (e.g. growing a brand new cell phone from scratch with a vanguard digital camera module).
Merchandise which might be unsafe, unreliable, or just not excellent don’t are likely to promote nicely (or for lengthy)
We at all times attempt to discover methods to maintain complexity and prices down, whereas sustaining design intent. There are a variety of how to try this (and John Teel from the {Hardware} Academy wrote nice recommendation on that matter right here).
Nonetheless, we regularly see folks attempting to hurry a mission, in an effort to please traders and potential prospects, with out giving adequate thought to their product design. And we have now seen a number of mission fail miserably due to that.
We will’t give examples from initiatives we labored on, for confidentiality causes. However let’s go over a few very excessive profile instances that led to issues of safety:
- Samsung was below huge stress to “beat” Apple by releasing the Galaxy Word 7 forward of the iPhone. They apparently skipped some testing, didn’t discover points with the battery in case of a drop on the ground below sure angles, and a few of their telephones began fires and even exploded. The corporate formally mentioned they misplaced about 5 billion {dollars}.
- Boeing was below excessive stress as a result of American Airways was planning to order Airbus planes (A320) for the primary time. They took a shortcut with the 737 Max, as an alternative of beginning a brand new design from scratch. Lots of of passengers misplaced their lives, and Boeing misplaced many billions of {dollars}.
A fast have a look at the CPSC or the Rapex web sites will yield many extra examples of lower-profile instances, amongst which:
After which, there are all of the instances the place the product failed too early and/or too typically with out inflicting security considerations. Poor reliability has killed many merchandise.
And all of the instances the place the product doesn’t do a ok job eliciting a optimistic suggestions from prospects/customers. That could be the No. 1 new product killer.
It should take a number of prototyping rounds to refine your product design earlier than you arrive at a remaining prototype
Over on the Sofeast weblog, we wrote in regards to the variety of prototyping rounds wanted to convey a brand new product to market, because the prototype iterations should be examined and validated.
As one iteration of the prototype product is examined, points will likely be discovered and corrected, leading to a second iteration, and so forth, till we’re lastly happy.
Quite a few samples per prototype iteration may even be made. By necessity, many assessments will injury or destroy the prototype because the product design’s limits are examined (very generally when testing reliability, after all).
Usually the assessments:
- Guarantee that the product works and appears prefer it must
- Show that the product might be made with the proper high quality
- Assess that it will likely be dependable for no less than the size of the guarantee interval, or longer relying on product kind and value
- Guarantee that the product is protected and compliant together with your market rules
- Verify whether or not the product will likely be broken throughout transit
The assessments will differ, however oftentimes they arrive from a certification particular to your product kind, though your provider’s check engineers could nicely devise a customized check plan in lots of instances, too, relying in your necessities.
Keep in mind, it took James Dyson over 5,000 hand-made prototypes earlier than he lastly had one which labored as he wished and may very well be developed till manufacturing was attainable.
You very doubtless received’t want hundreds of iterations earlier than you arrive at a remaining prototype like Dyson, however…
To count on perfection after creating one prototype iteration of your product design is to misconceive the position of prototyping. Prototyping is a course of we comply with to get to a prototype that appears and works as anticipated with the anticipated CMF. We could undergo a number of rounds of validation and product builds after the ‘first prototype’ is made, and every spherical will include many prototype samples that are used for testing. Over time points are discovered and stuck per construct till we’re happy and might lock the design, then turning our sights to mass manufacturing.
Good product design is difficult work
Merely plugging a number of components collectively in a means that makes it work is just not good product design. There’s much more work concerned, together with:
- Discovering out what the dangers are, from a utilization perspective, and translating that right into a reliability & sturdiness testing plan
- Discovering out what the problems will likely be, from a producing and high quality testing perspective
- Addressing these dangers by product design changes
- Getting the present spherical of prototyping, testing the prototype(s) to validate that there’s enchancment, and planing for the subsequent spherical
- Protecting the time and the funds for obligatory certifications earlier than mass manufacturing
- And lots of different duties akin to pre-selling the product, getting ready a advertising marketing campaign, elevating cash, discovering the precise producer, and so on.
Assets on this matter
We lined the prices of poor high quality and poor reliability in a podcast a number of months in the past.
We shot a video in regards to the ideas of sturdiness and reliability:
This video covers what designers must do as a way to improve product reliability:
Right here, we clarify what DFM and DFA imply and what they embody:
And on this video we clarify what DFQ is:
You might also take pleasure in listening to Why Skipping NPI Phases Is A Large Mistake and studying this submit the place you may see the NPI course of (which incorporates the phases the place lots of validation testing is carried out): Going from 1 Prototype to Mass Manufacturing straight is Harmful.
[ad_2]
Source link